Electric Car High Repair Costs Surprise Some Owners
It’s well known that today it costs more to repair an electric vehicle than a gas-powered car or truck. [Ed. Note: Hertz’ experience reinforced what many individuals have found.] What is less discussed is that rationale behind the challenges of EV repairs. With more EVs on the road today and those vehicles now beginning to show up in aftermarket repair shops, this shift in the automotive landscape signals a new era of challenges and opportunities for the industry. The recent launch of the Tesla Cybertruck a high-profile reminder of these challenges and opportunities with its stainless steel body and new technology. It’s imperative to explore the factors driving these cost differentials to understand how automakers may adapt to improve repairability, ultimately making the EV repair shop experience more cost-effective for consumers. A large number of repair shops today are actually unable to properly fix an EV because of their lack of knowledge and the limited expert diagnostic resources available.
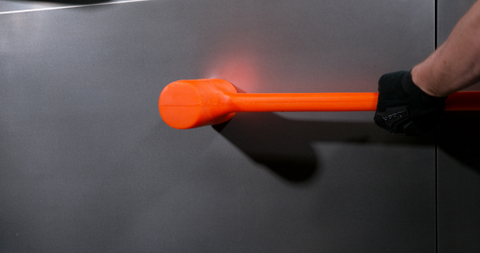
EVs are more technology-heavy than gas-powered cars. Particularly on the Tesla Cybertruck, with advanced features such as 48V electrical systems and steer by wire. Damage-resistant claims are being coupled with its technological leaps to revolutionize the automotive landscape and, in turn, the collision repair industry. However, the vehicle’s repairability will remain a question until there are more than a few on the road.
Critical areas such as the safety systems inside the vehicle, digital connectivity or the evolving materials’ complexity mean repair shop owners must find ways to navigate these significant driving forces in the escalating costs involved.
Safety Systems and Their Impact
One of the primary contributors to the cost disparity in EV collision repairs is the complexity of safety systems. EVs are equipped with an array of advanced safety features, such as collision avoidance technology, automated driving assistance, and the complex sensor networks that accompany these systems. While these technologies enhance safety on the road, they also add layers of intricacy to the repair process.
In the event of a collision, these safety systems can incur substantial damage, often necessitating specialized diagnostics, recalibrations and the replacement of high-tech components. For example, tires and suspension components may need replacements more often (because of EVs increased weight), which means these repairs will come with a heavier price tag compared to traditional combustion engine vehicles.
The scarcity of technician talent surrounding these specific repairs points to an issue–repair professionals must invest in training and external repair guidance resources to navigate these complex systems effectively and efficiently. This is seen in the explosion in the presence of mobile technicians and remote diagnostic services.
Digital Connectivity and the Repair Equation

The rise of digital connectivity in EVs has brought forth new challenges for the collision repair landscape. EVs often rely on intricate networks of sensors and computer systems to ensure seamless functionality.
In the aftermath of a collision, ensuring these digital systems are restored to their original state can be both intricate and time-consuming. It requires access to the right diagnostic equipment and software expertise. As a result, collision repair professionals must again invest in continuous training to remain proficient in this ever-evolving landscape, further contributing to the higher costs of EV repairs. Industry reports call for the reduction in vehicle collisions due to these advanced systems, but it is in the early stages of this change and the data has not yet confirmed these forecasts.
Materials Complexity and Its Implications
EVs are at the forefront of material innovation. Novel materials, including lightweight alloys and composite structures, are widely used to enhance efficiency and performance. While these materials contribute to the overall eco-friendliness and performance of EVs, they also bring a unique set of challenges to the collision repair process.
Repairing these advanced materials necessitates specialized training, tools and materials, all of which come at an added cost. Additionally, working with novel materials often extends the repair process, increasing labor costs and overall repair bills for EVs. The cost of materials themselves can also be higher, further widening the cost gap.
Adapting to Improve Repairability
As EVs continue to gain popularity across many OEMs, especially with the Tesla Cybertruck making headlines, it is crucial for automakers to recognize the evolving dynamics of the collision repair landscape. Addressing the challenges presented by the intricate safety systems, digital connectivity and materials complexity in EVs is imperative to get the aftermarket involved in EV repairs. Several strategies can help automakers improve the repairability of their electric vehicles, including collaboration with diagnostic solution providers, development of standardized repair procedures, accessibility to parts and materials, and overall innovation in processes and tools.
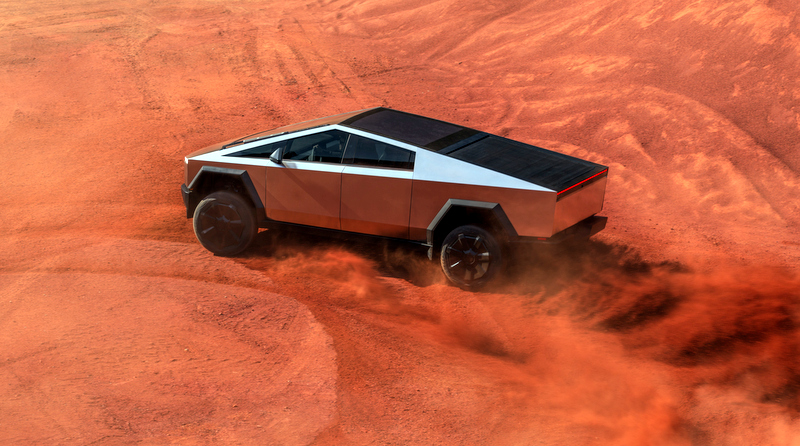
This very reason is why repair shops and their owners need diagnostic solution providers and expert resources that can help streamline the repair process and reduce costs, ultimately benefiting consumers. OEMs standardizing repair procedures for EVs can also simplify the repair process and ensure that collision repair technicians have a clear roadmap for restoring vehicles to their original state. Automakers should also ensure that collision repair professionals have access to affordable and readily available replacement parts and materials for EVs – even investing in research and development to create more efficient repair processes and tools, specifically designed for EVs can reduce repair time and, consequently, costs.
Overall, the cost gap between Tesla and non-Tesla EV collision repairs compared to conventional vehicles is a compelling issue that reflects the evolving landscape of the automotive industry as we head into 2024. Advanced technology, complex safety systems, digital connectivity and novel materials are pushing the boundaries of repair costs. However, these challenges also present opportunities for automakers to adapt and improve the repairability of electric vehicles. If you were to take 100 independent repair shops, about 85 of them today would be unwilling to work on EVs, which is why collaboration, standardization, accessibility and innovation are key to narrowing the cost gap among repair shops and making the EV experience more cost-effective for consumers. As the automotive world transitions to an electric future, it is the responsibility of automakers and collision repair technicians to pave the way for a more accessible and affordable EV repair ecosystem.
Change and opportunity are not just coming, they are already here driven by the technologies appearance in the aftermarket shop. Proactive shops that engage in training and the emerging services of remote and mobile diagnostics are the thriving shops of tomorrow.
The post Navigating the Cost Gap on Tesla and Other EVs for Collision Repairs first appeared on Clean Fleet Report.
[ad_2]
Source link